MyRideisMe.com Member Freebies! Welding Helmet
Member Benefits
If you don’t like free stuff. Stop reading now.
I’ve posted some how-to articles from the Lincoln Electric website in the past and since then have kept in touch with the well known welding brand. Lincoln even included at tiny MyRideisMe.com back in 1997 in their iWeld newsletter when we barely had any content. (Sure wish they’d do that again!)
So now, Lincoln has asked MyRideisMe.com to make sure these brand new Viking welding helmets go to deserving members. So how do you get one? (If you don’t want one, this might not be the right website for you!)
How to WIN one of these welding helmets:
- Members Only. If you haven’t signed up, click here to sign up now
- Members must have an avatar in their garage. (it’s easy, just click on it!)
- Maybe that’s enough rules.
Write a welding tip and leave it as a comment below. My Ride is Me is a community. Car people, in my experience are a friendly bunch and willing to lend a hand. Do that now and get some new gear!
- Tips or tricks you’ve learned
- Fables: Stuff you’ve heard that you know isn’t true about welding
- Welding horror stories (stuff to avoid)
- Your welding project, especially your hot rod, custom car or race car
- Not an expert welder (me either!) or just got a welder?
- Tell us how you picked your welder
- How will you learn to weld
- Show us why you bought a welder… What will you use it for?
- Surprise us!
I guess you could say, write something about welding that’ll help another member and you’ve entered to win the helmet. Any kind of welding is OK too… MIG, TIG or gas or whatever you’re good at, write it down.
Advice to win:
- Write a little and take a picture. Make it easy on yourself!
- Include a picture or pictures. Did I say to include a picture?
- Easy to understand is KEY. Bullets and lists are easy to read and retain.
- Use your own words. If I copy a phrase from your story and paste it into Google, I shouldn’t find an exact match.
When: The first of the 3 helmets (your choice of the 3 above) will go out the 1st week of April 2010. Submit your article as a comment below this story. Or, you can email it to admin at myrideisme.com (replace the at with “@”) no later than March 26th.
Some time in March, we’ll let you know how to win the other 2 helmets and probably the Optima battery we’ll give away EVERY MONTH starting in March. Have you signed up yet?
Any questions? Post them here! (you don’t have to be a member to leave a comment)
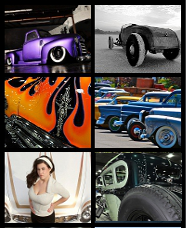
I’ll kick this party off…
When I’m welding, I like to -hey- Craig, knock it off, I’m trying to enter the contest! Did you put this “your computer will shut down in 2 minutes” message on my screen??!
I’m sure there are lots of welding tips floating around…
I will keep these helmets for myself!! How hard is it to say,
“Close your eyes when you’re welding!”
Cool Site
I hope no one needs this tip, but it,s a great one. It’s an old time remedy for severe or moderate flashburn. You can get flashed pretty bad even from a reflection if things are just right (or actually wrong!) Usually it comes on a while after you’ve been flashed, like after you go to sleep. If you have been flashed good you know what I mean. You will feel like someone held your eye open and poured sand in it. No relief open or closed! A very ugly feeling. Forget att the storebought stuff, just grab a raw potato and shred it like you are making hash browns. Trust me this works. Get a wad of the freshly shredded spuds and lay back and place a wad about golfball size or bigger on each eye. You don’t have to open your eyes, the juice will seep in lightly when you relax. Do this for about 30 minutes and you should be good to go. I’m not a Doctor, I’m a welder so you can’t come after me if you turn into a french fry. Try at your own risk, IT WORKS.
Thanks for that tip! See, that was easy!
Recently broke off a std in an aluminum engine and after much frustration trying everything that didn’t work and finally breaking off the easyout as normal, I took a nut and held it centered over the broken bolt & welded it to the stud with my Lincoln wire feed. This time I had to redo it 4 times but finally it came out.
Welding 101, don’t watch the arc, or the center where the arching is occuring. Watching the edge of the puddle will tell you much more about your heat, the welding rate and the watching the back edge will tell you that you have tied the two peices together! Preperation is key, the peices to be welded must be clean and free from rust, paint and grease! Also make sure where you attached the ground has been cleaned for a good connection, an arching ground will make your starts difficult and you might end up with more spots to repair!
Welding 102- welding creates heat you must manage. Too cold and there is poor bonds, too hot and you burn through and have a BIGGER mess to repair. Managing the amount of heat you induce into the work or component critical for a good end result. You must understand that as the weld cools the work will draw materials towards where it was welded. So you can account for the draw or warpage and set up the parts so they draw into the correct position? This is hard to do and take experience. You can manage the heat and weld a little at a time, or better yet is if you can weld on both sides then tack and weld skipping front to back or from one end to the other managing the heat you inject into the project. This will help you maintain the intended dimensions.
WHen mig welding for strenghth.use the hot spot method. It is done by using a bunch of spot welds. right after one another instead of using a bead. This will produce a joint that is almost as strong as a tig welder.. and done properly it will look like a stack of dimes layed on there side..
Why is a tig weld stronger then a mig weld???
Answer:
Its not.. the weld is not any stronger. it is the metal around the weld that is stronger beacuse of less heat…..
The most simple tip that any new welder should know is to take your time, and space out your tack welds along the perimeter of the patch panel, secure all sides with a few tacks then move around the patch tacking small spots keeping as much distance between them as you can, this will reduce the amount of heat put into the steel at any given point and will help reduce warpage of the material.
Also, never quench your welds with water or oil or a rag as you can temper the weld or the steel where you welded and cause it to crystallize and become brittle or even make it crack.
I hope these were okay, I’m a pretty new welder, but have been having pretty good success… I just wish I had a helmet because those sparks are hard on my sunglasses! :p
Everyone leaving a comment should already be a member. Leaving the tips here in the blog is OK. Or you can send them to me by email. Thanks!!
Becoming proficent at welding is all about practice, so gather every scrap of metal you see. Along the road, in fields, down alley’s, not only will you have practice material, but you will help the environment.
Use a good welding helmet while you weld. Not only do they save your eyes they really help you pick up chicks…
When using my Lincoln Sp125 i checked to see how many Amps the welder can use and make sure the power source is putting out the correct Amps. By doing this your duty cycle will go up and your ability to adjust the welder will be increased.
A second tip is to make sure your material is clean and you are using the correct gas for your material. There are several gases that will allow you to weld, but picking the correct gas allows for a better and cleaner weld.
Rocky
When filling a hole or gap in metal and need one side smooth or to help cut down on grind time, I use a few sticks of soap stone on the back side of the hole by placing to the metal and keep them in place untill the hole is filled so the pool of metal does not fall through the hole and the it will not stick to the stone. This will work on any typ of metal.
Hope this will help.
Thanks, Robert Hall (RED)
I learned this the hard way, on my roof had a hole and cut a square out and to replace with a square. As I started welding that it I got it too hot and warped the metal. I should have used a round piece that way the heat can be spread out more and not pull into a corner!
Another lesson, sparks will burn through a shirt or a blanket and burn your cloth seat!!! For some reason I thought it would slow down any sparks or embers but it was too late before I realized my mistake! Don’t rush or get in a hurry!
When you’re using your wire feed welder to fill in holes (like in a fender when eliminating trim or similar task) use a scrap piece of copper behind the hole to be filled. The copper keeps you from burning the edges of the hole and keeps metal from falling behind the weld. Also, your weld won’t bond with the copper scrap.
I’m not sure of the proper name,but i was having problems with my mig wire sticking.My lead got dirty inside the line, it splattered and wasn’t welding very good. A friend of mine showed me something I wasn’t aware of… It was a round sponge that you soak with a special lubricant. It goes on the wire inside before it goes through the feeder of your mig welder.Keeps inside liner lubricated and free of debris.It really helped and made good welds. People ask now,who welded that? Good looking weld!
Nice Michael. Can you find out what that lubricant for the wire is? Anyone know? If you’re a member, you’re now entered to win the helmet!
Sir,in response to lubricant used for mig welders. The name of it is Lube-Matic Kleener.
Wire-Kleener
Increases Tip and Liner Life
Removes Dirt
Cuts RUST Decreasing downtime due to jamming
Reduces wire drag by 60%
MFG. Weld-Aid Products
to push or pull? I’ve found pulling the weld allows me to view how the weld is penetrating the metal and when to move on. Another huge factor is having the metal free of paint, rust, or any other foreign object. You think the heat will burn off the items but you get a much better weld when you take the extra time to prepare before you weld.
If you are in the automotive hobby, and if you’re reading this you most likely are, one thing that becomes apparent relatively soon. You realize that you will need to have either a large amount of expendable income or many skills and patience to learn them. For me, having large amounts of extra cash is not something that I have control over, but learning and practicing and acquiring new skills is something completely in my control. That is great news!
If you are an automotive hobbyist and not well endowed financially, I would say that learning to work with metal is a must and worthy of any time you invest in it. (Cars are made out of metal, or at least they used to be). Labor rates to get quality metal work done can reduce your dreams to a few bolt on accessories.
Below was my plan of attack to gain as much immediately useful, real-world knowledge in the shortest amount of time. I have done this in the past to learn body and paint and in the future I will use this plan of attack once again to learn upholstery.
If you want to learn to weld, learn from the best. Look up and visit weld shops in your area and find the most gifted artisan that you can.
Try to find a shop that does a large variety of work as opposed to one that makes thousands of one part. When you have found this particular person, make him/her an offer they can’t refuse. Set it up if possible, as a semipermanent rotating schedule. I.e. every Friday or every other Friday from noon to 4 PM. This will keep you going when enthusiasm wears off and gets rid of the clunky effort of trying to set things up each time you meet. My offer was this: I will show up on time, I will bring you lunch, I will clean your shop and I will help you with any task you like and will even run to the store and get your cigarettes when you run out.
I ask for no financial compensation only to watch you work to have the freedom to ask you questions about what you’re working on.
You may feel awkward about it for a while. Don’t sweat it but just be as helpful as you can. Just go with it knowing that it will eventually smooth out.
I ended up with access to the scrap metal pile, which can be rather substantial at a large shop, and was even able to borrow shop equipment to bring home to work on my car which was on Jack stands. I would get five or six great tips visually demonstrated per day. I would work on my own parts at the shop and have them critiqued which maximizes the learning experience. You always seem to be able to remember somebody pointing out an error that you made. Use your human frailty and insecurity to your advantage! :-).
I have worked on everything from a super heavy duty flash pan for the United States Navy to explode their unused ammunition, various aerospace and missile parts, repairing vintage transmission casings, go carts, antique rocking horses had a few other industrial things that I have no idea what they do.
So… I have written all this and there is not one actual tip listed…
*Copper is good. It will draw heat away from areas where it is not wanted.
*Clamp, clamp and clamp again. Have some of every kind of clamping device ever made handy. (You may want to stay away from the plastic ones)
*CLEAN METAL! At least three-quarter inches back from the bead.
*Bevel edges for maximum penetration.
*When joining a thick piece of metal to a thin one, put your heat into the thicker piece.
*If possible, join pieces corner to corner. (Inside corner to inside corner) this maximizes surface area and allows you to dress the weld without grinding away the strength in the bead.
*Half of welding is grinding/sanding. Seek to improve your technique here.
*Even the best experts make mistakes. Don’t be afraid to take something apart and start over. This better than constantly fighting with something to get it to work.
Peace,
Kai
when welding on a patch panel such as a rocker or a quarter panel position it with clamps and then use self tapping screws to hold the panel in place. Be sure to drill holes between the screw holes for spot welds. Then after you have welded all of those plug welds, take out each screw and weld those holes shut as well.[IMG]http://i22.photobucket.com/albums/b350/wingwalker87/patch_panel.jpg[/IMG]
The key to good welding is understanding what you are seeing through the helmet lens and controlling what is happening there (size & shape of the puddle, penetration, etc
http://s168.photobucket.com/albums/u183/ChopperDaveDesign/1919%20Chevrolet/?action=view¤t=IMG_2074.jpg
I’ll share a few things I’ve learned along the way. These tips pertain to MIG welding on a car specifically.
1. You don’t need a monster 220v welder to work on a car. Think about it, the thickest material on your car is probably the frame rails, and its probably .120″ (1/8″). I’ve gotten by with a Hobart 140 amp 110 volt welder for years, and never wanted more power. Just make sure you are plugged directly into the outlet and that you have a 20 amp breaker. Usually your garage will have at least one 20 amp breaker. If not, plug into your washer/dryer outlet. If you have to use an extension cord get a heavy duty one, mine’s a refrigerator extension cord that I got at the home improvement store for less than $20.
2. Use C25 gas, which is 75% Co2 and 25% argon. It will get you a cleaner weld and is worth the extra expense. Speaking of bottles, buy the biggest one you can afford. You are paying for the fill, not the gas. A small bottle might be $40 to fill, and a big bottle with 5x the gas could only be $60. It’s worth calling around too, prices vary wildly. Always turn the bottle off when you’re not welding or you will leak out all the gas in no time.
3. I’ve found that .023 wire works best for sheetmetal and all around welding. If I’m going to be welding a lot of heavy wall material (.120″-.250″) I’ll put in a roll of .030 wire. I don’t see a need for .035 or larger on a car ever. Also, buy name brand wire such as Forney or similar. Harbor Freight wire seems to come with impurities in it, leading to crap welds. If you throw down a porous, contaminated weld you might as well not weld at all.
4. Speaking of crap welds, make sure everything is super clean before you put down even one tack. That means the front AND back of every piece you weld. If you are welding on the sheetmetal on your car this is critical. Find a way to grind the paint, undercoating, rust, bird poop, whatever off the back side of the workpiece. If you don’t you will have a porous contaminated weld. There are two problems with this: First, the weld is not strong at all. Second, if there is a pinhole in the weld it can allow moisture in from the back side of the panel and ruin your paint from the inside out.
Fully seam welding a first or second gen Camaro sub-frame can stiffen it and make it stronger, however the frame is made of two halves that overlap at the seam and oil and grease can hide there causing poor welds, smoke and pin holes.
Take an Acetylene torch, warm a 6″ long section to just a couple of hundred degrees, if there is oil it will create smoke, hit the oxygen cut lever (30 PSI) to blow out and burn out any oil residue. The excess oxygen in cut mode will cause the oil to burn and if there is a lot, it will splatter around so do this in a safe area. Keep the torch moving and 3 to 4 inches away from the frame, don’t heat the frame red hot, just barely warm it. This technique can quickly remove paint and oil from any metal surface. Just wire brush off the soot when done. Many older paints contained led, red paint is particularly noxious, so keep your face out of the smoke.
When welding the sub-frame, do 4 inches, then move to another spot far away on the frame, take a break after doing 4 welds, and don’t overheat the frame, don’t make the weld bead too wide or heavy, the excess heat can warp it.
it all boils down to clean metal and fitup being key…and lookin as sexy as possible in tight jeans while workin. what? chicks are allowed to weld too!
I have a quick one. Clean it up before you weld it. The guys i work with will turn the welder on and they will weld it up. No cleaning it. When I weld I like to clean it all up then weld it even if no one can see the weld after it’s all done. Thanks
If you have to weld in a tight spot, but there’s nowhere else to clamp the ground, use a set of needle-nose vise grips. Clamp the vise grips to the workpiece, then attach the ground to the vise grips.
when you weld with a darkening helmet and you find you can’t see where your welding ,use a halogen lamp over your shoulder and adjust it so you can see prior to the helmet lens turning dark.
1) When welding overhead always, ALWAYS, make sure your collar is completely secured and there isn’t any room for slag to fall between your shirt and your skin. Trust me, the trail of little round scars isn’t worth it.
2) If you failed to follow #1, or the stars just aren’t aligned for you, don’t suck in your gut as you react to the slag rolling down your chest and abdomen burning you in a new spot every step of the way.
3) If you failed to follow #1 and #2, or the asteroid that is going to destroy the earth has recently been given your namesake, undo your pants immediately and get that darned hot piece of metal out of there, like, yesterday!
4) If you’ve made it this far you are now pants-less hopping around the shop chanting your favorite expletive. You are on your own. Like I said, you’re pants-less.
LOL!! Thanks Jack! ‘Bout time we had some humor! Welding’s fun!!
We all know that clean metal welds better.
But when learning to weld, after getting fair at clean metal, start welding some dirty scrap together. Dirt, rust , paint, etc. There is a method to this madness. After you get decent as welding nasty junk together, go and do some clean metal. That self taught technique for getting a decent weld in junk will make welding nice metal come out much better. Nothing like a little adversity to improve the product
Good one, Jack! I have burn holes in my underwear from mig welding while sitting down.
Won’t do that again…
dw
don’t weld when your wearing your nylon swim trunks.
i’m a newbie welderette.
only a couple of months and so very green.
just learning on a cheapo 110 stick welding machine.
want to see if i can really get the hang of this before i take the plunge and get a REAL machine :)
would love to be the girl that the guys in the neighborhood sheepishly came to when they need something welded. heh. heh.
welding guru that has taken me under his wing, hates my old school non-auto lid ’cause i can’t see what i’m doing!
(he really loathes the flower stickers i’ve put on it too)
i have been pinchin’ pennies for an auto-darkening helmet to make guru happy.
help a girl out, so guru will quit grumbling.
i have personal ‘sperience with two tips……
#1) if you have small hands, get gloves that fit!
gigantor clown gloves make learning miserable. get gear that fits you right!
#2) pull your hair back or it will catch on fire. i’m okay…really.
i am really appreciating all the tips and wisdom!
way helpful. seriously.
Any idea on when we will find out who wins the helmet???
I learned the hard way to turn off the gas tank on the welder. A brand new tank disappeared into thin air, $50.00 later a fresh tank and a sign on the wall saying turn off gas when finished. So far it’s worked.
tuc pant legs in to the boot so when you weld slag wont get into your boot
When doing a vertical up position weld with Flux Core Arc Welding, set amperage between 20.5 and 21.5. Set the wire speed to about 3. Keep the electrode extension to around 1/8th of an inch from the nozzle. Beginning the arc is easy, keeping a constant weld size and quality is the hard part. Remember to always keep the FCAW gun straight, therefore you will be able to see your weld pool and the rate of which weld is deposited.
Appreciate your efforts for informing us about brand new viking welding helmets information. Thanks for nice tips.
Well i aint really big at the writing thing but a trick i learnd in school that a friend tought me was to get any rod break the flucks off and while your welding you put it in any gap and it will fill the gap for you.Well thats about it for know im just starting off but later when i get experience ill write yall back.
I have been MIG welding for about 3 yr the best way to weld with hard wire u need push ur puddle and with flow core u pull ur puddle and to do aluminum u push ur weld forward if u drag ur puddle it goes black
just starting out and finished school, thanks for the tips
When arc welding try to find your special touch or right speed and technique to ensure a strong weld.
When welding an out let to a pipe for fire protection sprinkler tack it of course an use the paint brush technique an pull the weld an ur weld will come out clean an make sure ur heat an speed is at the right setting mine r 24.0 heat wire speed 383
Take pride in all your welds.Your weld say who you are as a welder.
Just gotta say, angle and travel speed is everything! Gotta make that penetration at just the right speed! – Mrwelborn58
Alway’s watch you angle and puddle build! Ensure you use the proper travel speed as well!